30L Plastic Watering Cans Blow Moulding Machine
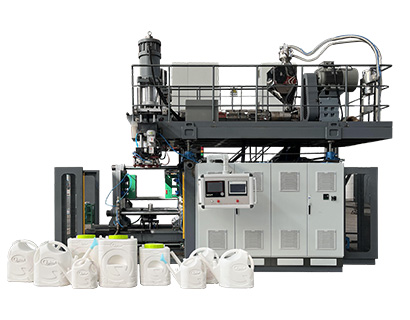
The 30L series extrusion blow molding machine is used to produce all kinds of hollow plastic containers for foods, toys, beverages, medicines, chemical products, pesticides, detergents, etc with the material of HDPE, PE, and PP from 1L to 30L, such as watering cans, jerry cans, stacking barrels, fuel tanks, and plastic containers.
The machines are low investment, high efficiency, quick and safe operation, easy for troubleshooting, maintenance and another benefit.
Delivery Date:2-3 Month
Technical Parameter of 30L Plastic Watering Cans Blow Moulding Machine
Technical Data for YK 30L Series | |
Model No. | 30L |
Screw Diameter (mm) | 90 |
Screw L / D ratio (L/D) | 25/1 |
Screw drive power (KW) | 30 |
NO.of heating zone (zone) | 4 |
Screw Heating capacity (KW) | 20 |
Output of HDPE (kg/h) | 80-110 |
Main Oil pump drive power (KW) | 15(22) |
Max Mould Size (mm) | 800*850 Or customized |
Clamping Force (KN) | 260 |
Max. diameter of Die head (mm) | 100-240 |
Die head heating power (KW) | 18 |
NO.of heating zone of die head (zone) | 4 |
Blowing pressure (Mpa) | 0.8 |
Air volume (m3/min) | 0.8 |
Cooling water pressure (Mpa) | 0.3 |
Water consumption (L/min) | 60 |
Total power (KW) | 80 |
Dry cycle (pc/h) | 600 |
Size of machine (LxWxH)m | 4.2*2.2*3.3 |
Weight of machine (TON) | 12 |
Applications of 30L Plastic Watering Cans Blow Moulding Machine
The 30L plastic watering cans blow moulding machine can be used to produce 1L-30L plastic products, including but not limited to water tanks, jerry cans, buckets, kettles, hollow seats, etc. The blow moulding machine can produce various thin-walled hollow products, chemical and daily packaging containers, as well as children’s toys, etc.
Configuration of 30L Plastic Watering Cans Blow Moulding Machine
①Leading International Technology
For example:
Use original SIEMENS control systems. Guarantee high quality, safe and stable operation. At the same time, it provides after-sales international services.
For more advanced configurations, please refer to the following figure.
SR | Description of Parts | Brand | Origin |
1 | PLC | SIEMENS | Germany |
2 | Touch Screen | SIEMENS | Germany |
3 | Inverter | SIEMENS | Germany |
4 | Screw Motor | SIEMENS | Germany |
5 | Air Switch | SIEMENS | Germany |
6 | Contactor | SIEMENS | Germany |
7 | SSR(Solid State Relay) | CARLO GAWAZZI | Switzerland |
8 | Wall Thickness Controller | MOOG | USA |
9 | Servo Valve | YUKEN | Japan |
10 | Hydraulic Valve | YUKEN | Japan |
11 | Solenoid Valve | YUKEN | Japan |
First, the multi-layer mold design makes the wall thickness uniform and stable. Second, it can increase production efficiency by 5 times. Finally, the utilization rate of recycled materials increased by 4 times.
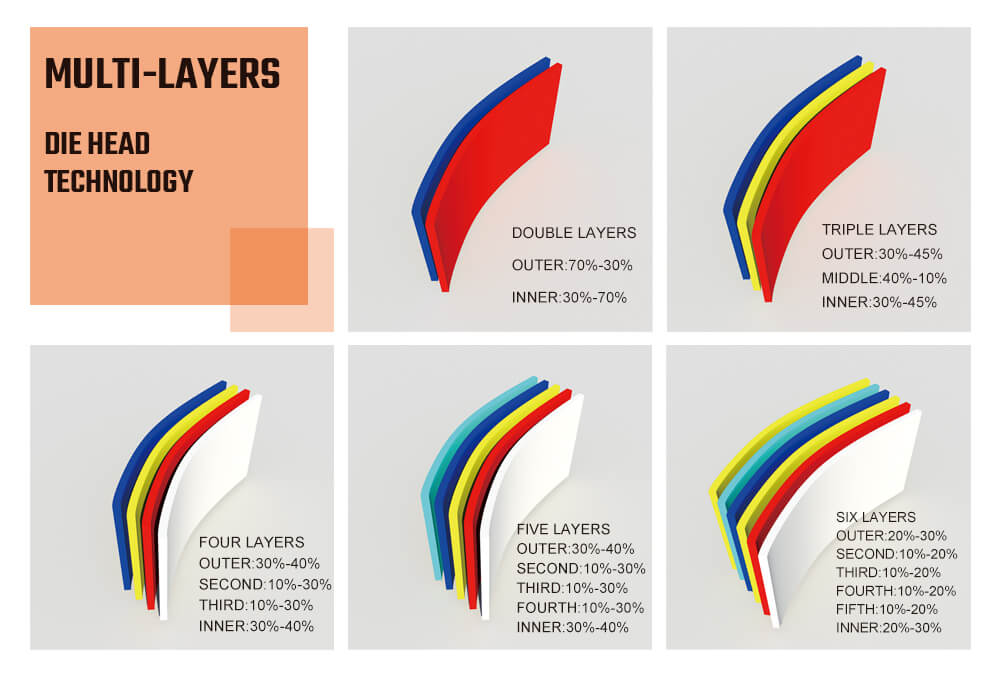
Customer Service
①Training
The buyer could dispatch their operators to the seller’s factory for training, including machine operation, maintenance & simple repairs;
Or against the requests of the buyer, the seller’s technician could train the buyer’s operators in the buyer’s factory in the periods of installing & adjusting;
②Installation & Adjustment
The seller could dispatch an engineer against the requests of the buyer to install and adjust the machines for one week(free of charge) in the buyer’s factory. After one week, if the buyer still needs the training,$100 should be paid to the engineer.
The buyer should make a reservation in advance before the delivery of the machines;
The buyer should pay for the engineer’s food & board while installation in the buyer’s factory. And the buyer should also pay for the air ticket for the engineer.
③Guarantee
The guarantee time is 1 year after the machines normally work in the buyer’s factory if only the problem is caused due to quality control or any reason by the seller. We will supply replaced parts free of charge and our engineers will guide you on how to solve the problems.